Referenz - Firma KUKA AG
Betriebsausstattung für Messraum kommt aus dem Schwarzwald
Bedrunka+Hirth in enger Zusammenarbeit mit Fachhändler Werkzeug Weber in Aschaffenburg
Während Outsourcing branchenübergreifend in aller Munde ist, investiert die KUKA AG gegen den Trend über in den Standort Obernburg. Mit der neuen Präzisionsfertigung konnten Lieferzeit und Kosten erheblich gesenkt werden. Die Umsetzung stand unter Zeitdruck. In nur drei Wochen schafften es die Betriebsaustatter aus Aschaffenburg und dem Schwarzwald gemeinsam, das Projekt von der Planung bis zum Aufbau umzusetzen, pünktlich zu einem Treffen der weltweiten Geschäftsführer.
Mit der Übernahme des Mittelständlers Reis Robotics durch KUKA begann der Konzern die Neuausrichtung der hinzugekauften Werke. Jeder Standort und dessen Portfolio wurden auf Stärken und Schwächen analysiert. Mit dem so gewonnen Profil wurde ein Konzept erarbeitet, wie sich die Unternehmen gewinnbringend in die Konzernstruktur einbinden lassen.
Die Stärke des Obernburger Standorts ist die Fertigung. Die Erstellung von hochkomplexen Teilen, bei denen es auf die Präzision ankommt, hat hier eine lange Tradition. Ob für die Solarindustrie, Automobil oder Raumfahrt: Lösungen aus Obernburg finden weltweit in der Spitzentechnologie Anwendung.
Im Oktober 2018 viel die Entscheidung: Die Fertigungskompetenz für hochpräzise Teile soll ausgebaut werden. Über eine Million Euro wurde zur Investition freigeben. Ziel war es, die Beschaffungsgeschwindigkeit für die entsprechenden Teile im Konzern zu senken und dabei Kosten zu sparen. Projektleiter am Standort Obernburg ist Michael Stierhof. „Bis zur Bewilligung war es ein langer Weg.“, erinnert sich Stierhof. „Aktuell ist Outsourcing im Trend. Wir haben einen Vorschlag zum Insourcing vorangetrieben und sind gegen den Strom geschwommen. Da waren viele Gespräche notwendig. So eine kritische Betrachtung des Konzepts hat auch gute Seiten: Unsere Idee wurde mit dem Input weiterentwickelt. Und wenn ein Konzept einer solchen intensiven Prüfung standhält, spricht das auch für die Güte der Idee.“
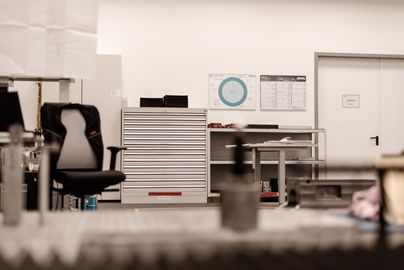
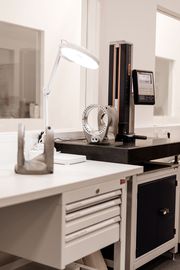
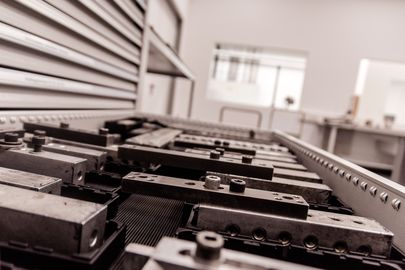
Das aus Managersicht ungewöhnliche Vorhaben machte dann schnell die Runde im Konzern und führte zu einer neuen Herausforderung, wenn auch eine angenehme. Die runde der weltweiten Geschäftsführer von KUKA entschied sich, ein Treffen in Obernburg zur Begutachtung der neuen Präzisionsfertigung zu machen. „Eigentlich lagen wir sehr gut im Zeitplan.“, erinnert sich Stierhof. „Um das Treffen der Geschäftsführer möglich zu machen, mussten wir jedoch das Tempo steigern. Schließlich war dieser Besuch für unseren Ansatz eine große Chance, wir wollten uns konzernintern als Lieferant für Präzisionsteile positionieren.“
Herzstück einer Fertigung für Präzisionsteile ist der Messraum. Während sonst in der Fertigung Kontrollen nur nach vorgegebenen Stichproben je Charge stattfinden, werden Präzisionsteile zu 100% geprüft. Die Fertigstellung des Messraums lag planmäßig eher am Ende der Maßnahme. Und hier musste bis zum Treffen der Geschäftsführer nun besonders Gas gegeben werden. Zur Einrichtung des Messraums war eine Vorbesprechung im März 2019 angedacht. Anfang Februar klingelte das Telefon von Marco Welke, Gebietsleiter bei der Werkzeug Weber GmbH & Co. KG in Aschaffenburg. Von der Besprechung bis zur Inbetriebnahme des Messraums blieben nur drei Wochen. Da muss jeder Handgriff sitzen.
Umgesetzt wurde die Maßnahme mit Bedrunka+Hirth. Die Spezialisten aus dem Schwarzwald fertigen seit über 40 Jahren in Bräunlingen Einrichtungen für die Industrie, Handwerk und den Dienstleistungssektor. KUKA wählte zur Aufbewahrung der Messwerkzeuge einen Schrank mit gedämpften Auszügen für die Schubladen, ähnlich wie man es aus dem Wohn- und Küchenbereich kennt. Das Softclose System schützt empfindliche Teile vor Erschütterung.
Die jahrelange, eingespielte Zusammenarbeit machte sich bezahlt. Dem Ensemble gelang es, die Ausstattung nicht nur fristgerecht aufzubauen, sondern auch noch in Sonderfarbe zu liefern.
Den Geschäftsführern von KUKA konnte eine topmoderne und vollfunktionsfähige Präzisionsfertigung vorgeführt werden. Nach rund einem halben Jahr im Betrieb kann man sagen, dass die Lieferzeiten der Spezialteile erheblich gesenkt werden konnte und die Kosten merklich reduziert. Ein Modell für den Standort Deutschland und dem Label „Made in Germany“.