Workplace 4.0 - The assembly site of the future
If current studies are to be believed, the demands placed on modern workplaces are transforming in a disruptive manner and, at that, significantly faster than experts ever predicted. The digital revolution has already reached broad sections of companies and is continuing with unbelievable dynamism. Everyone involved – entrepreneurs and employees alike – are being called upon to see these changes as an opportunity. All processes need to be thought over and put to the test. Artificial intelligence is reshaping the environment and workplace design in virtually all sectors. Computer systems are working hand in hand with their human colleagues. Process chains are being broken up and restructured on the basis of cognitive ergonomic criteria. All parties involved are required to obtain advantages for companies and employees from this in order to successfully help shape the digital revolution.
From challange to opportunity
Every day, your company’s employees grapple with strenuous tasks and heavy physical labour. This often poses great challenges to employees. The performance of your company depends on how motivated and fit your workforce is, as well as on how up-to-date and competitive the skills of your employees are. The critical competitive factors are no longer economy and technology. It is demographics. Here, the person is in focus!
Above all, older and unskilled employees will benefit from the new technological possibilities. Thanks to smarter assistance systems, they will be capable of being active in industrial production for longer, as machines will relieve them of their exhausting work. For Bedrunka+Hirth the motto is “The person is in focus – the technology assists”. The person is supported by intelligent machines. Bedrunka+Hirth wishes to realise these objectives to turn Industry 4.0 into something tangible.
Cognitive ergonomics
The constantly growing number of variants and rising quality requirements are gradually increasing the mental stress on an employee to know and implement the respective work steps correctly. Easy to set up visual instructions let each employee know at all times which work step has to take place next and with which article. The visual check relieves the employee from the stress of having possibly installed an incorrect component in the wrong order.
Mastering complex work
With a height-adjustable worktop, we ensure good ergonomics. The combination of intelligent software and an ergonomic workplace relieves the employee in every respect. The assistance system is employed along the entire value chain: From incoming goods to assembly to outgoing goods. The possibilities range from mere identification to a fully equipped incoming goods inspection with supplier-related sampling selection. Depending on the customer’s requirements, these modules are unified into a single system.
Workplace 4.0 - The equipment
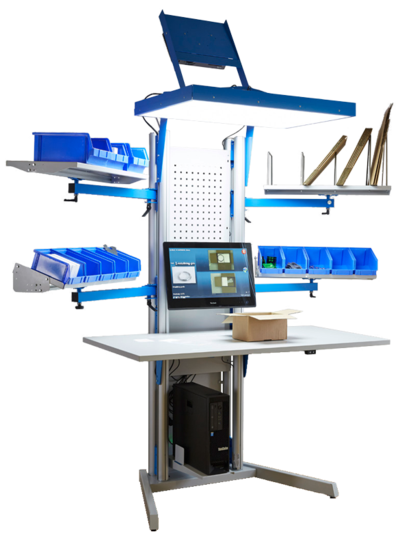
- Table frame with aluminium profiles, height adjustment synchronous with 2 motors in the aluminium columns
- Worktop max. 1500 mm wide, height adjustable from 720 to 1030 mm. Fixed distance between worktop and top frame with camera of 1210 mm
- Front with perforated sheet metal casing for screen bracket, rear with housing for cables
- Setup for beamer (for 3D application)
- Load capacity of tabel top: 160 kg
- Administration of employee, parts and packing/assembly lists
- Learning module with free selection of features
- Database for master data with associated images and features
- Search function for documented assembly, packing or inspection processes
- Packing or assembly lists are created by drag and drop
Workplace 4.0 - The possibilities

Guiding
The employee is audiovisually guided through the process via the touch display and is shown what work steps are necessary. This means that: All new employees can already manage the process safely and correctly after a short period of training and without lengthy work instructions. Employees can be deployed without prior knowledge and with considerably greater flexibility. Processes are more reliable, errors are prevented, and psychical stress never even occurs in the first place.

Checking
With the help of the camera, the system checks whether the work step has been performed correctly. In the process, each substep is automatically checked so that errors can be prevented directly at the source. A 100 % check is ensured by the integrated QS. Measuring, weighing, counting and identifying take place in real time in seconds.

Confirming
After each inspection, optical and acoustic signals are issued directly to the employee. If the task has been completed correctly, the system confirms this with “OK”. If the employee makes an error during assembly, the system issues an acoustic signal and additionally instructs him to execute the step correctly.

Documenting
Every correctly executed work step is automatically saved as an image; in the process, the body parts of the employee are detected by hand tracking, but not recorded. The complete and correct execution of the process can thus be proved at any time. Product recalls, costly complaints, and subsequent consignments of missing parts are a thing of the past.
Workplace 4.0 - In use

Example assembly
The constantly growing number of variants and rising quality requirements are gradually increasing the mental stress on an employee to know and implement the respective work steps correctly. The visual step-by-step guidance via the display immediately lets the employee know which work step has to take place next and with which article.
The visual check relieves the employee of the stress of having installed an incorrect component or of having performed an incorrect work step.
The advantages:
- Step-by-Step Guide
- Guidance through text, images and videos
- Release only when the work step has been completed correctly
- Integration of torque, weight or other test and measurement data
- Control of machines

Example picking lists
Recurring complex packing processes with partially very similar products are ergonomically displayed to the order picker in large images on the workstation. The employee knows at all times which part to pack next, how to pack it and the system automatically checks that the employee is packing the correct part (and not a very similar one by mistake). With the image documentation, it can be proven to the customer at any time that the correct part has been completely shipped.
The advantages:
- Omission of the training time
- Prevention of mistakes
- Automatic documentation
- Discharge of the employee
- Increased customer satisfaction
- Detailed production data acquisition

Example check
For products where a large number of similar parameters have to be checked, the system helps to identify the correct parameters and to ensure that there is no confusion. In addition, the system can count features, measure weights and include and document other technical parameters in the check.
The advantages:
- Securing the QM specifications
- Step-by-step documentation
- Signalling of detected faults
- Traceability
- Interfaces to other programs possible